Date | Venue | Fee | |
---|---|---|---|
15 Sep - 19 Sep 2025 | Dubai – UAE | $ 4,950 | Register Now |
01 Dec - 05 Dec 2025 | Barcelona - Spain | $ 5,950 | Register Now |
08 Dec - 12 Dec 2025 | Barcelona - Spain | $ 5,950 | Register Now |
16 Feb - 20 Feb 2026 | Amsterdam - The Netherlands | $ 5,950 | Register Now |
25 May - 29 May 2026 | London - UK | $ 5,950 | Register Now |
14 Sep - 18 Sep 2026 | Dubai – UAE | $ 5,950 | Register Now |
30 Nov - 04 Dec 2026 | Barcelona - Spain | $ 5,950 | Register Now |
About the Course
To produce an inspection scope, one can use either of the following four criteria: time, condition, consequence, and risk.
A time-based inspection scope is the easiest to create and the cheapest to maintain; however, like a consequence-based inspection scope, it does not offer any corrosion failure pre-emption capability. On the other hand, a condition-based inspection scope does offer partial capability. If an operator is interested in establishing a corrosion failure pre-emption capability, then a risk-based inspection scope is the solution. It might require more resources compared with the other three inspection types, but it can nevertheless help to reduce the number of corrosion leaks and failures. Thus, a risk-based inspection could further optimise the associated corrosion and integrity costs. To create a risk-based inspection scope, one requires a failure risk assessment (FRA) procedure or methodology.
This 5-day practical Risk-Based Inspection in the Upstream Oil and Gas Industry training course provides the delegates with a semi-quantitative FRA methodology, enabling them to fully appreciate the main pillars of a typical FRA process. Such training would further enable them to create a semi-quantitative FRA methodology to serve any possible asset and scenario.
Core Objectives
By the end of this training course, delegates will learn to:
- Appreciate concepts such as threats, likelihood, consequence, failure, hazard, operability, and risk
- Estimate or calculate the associated likelihood, consequence, and risk values
- Design and create a bespoke FRA procedure suitable for their asset
- Choose and use a particular FRA option more suitable for their needs
- Improve their corrosion failure pre-emption capability via a bespoke FRA procedure
Training Approach
This training course will be delivered via PowerPoint slides containing text, tables, plots, pictures, etc., and it will be interactive; the delegates will be asked to participate regularly in an ongoing topic, discussion, or challenge. Various RBI case studies will be presented throughout the program as exercises, helping the delegates calculate the associated risk values and inspection intervals.
The Attendees
This training course is open to anyone involved in planning and executing an inspection work scope and eventually processing the inspection data. It will facilitate all operators and their inspection departments who intend to move from time—or consequence-based inspection to risk-based inspection.
It will be valuable to professionals, including (but not limited to) the following:
- Corrosion & Integrity Engineers
- Production & Operation Engineers
- Inspection Engineers
- Repair & Maintenance Engineers
- Asset Project Engineers & Asset Managers
Daily Discussion
DAY ONE: INSPECTION BASICS AND ANOMALY MANAGEMENT SYSTEMS
- Introductions
- Scope, Objective, and Attributes
- Definitions
- Why do We Carry out Inspections?
- History and Evolution of Inspection Types
- Advantages and Disadvantages of Various Inspection Types
- The Main Inspection Parameters
- Inspections and Anomaly Management Systems
DAY TWO: THE RISK AND FRA BASICS
- The Risk Concept
- Integrity Threat Categories
- The Failure Risk Assessment (FRA) Methodology
- The Relation between FRA and RBI
- Various FRA Types
- The Required FRA Input Data
- Typical FRA Outputs
- Risk Codes and Inspection Intervals
- Inspection Confidence Grades
DAY THREE: CORROSION LOOPS, PROCESS FLOW DIAGRAMS, AND RELEVANT STANDARDS
- Determination of Corrosion Loops/Circuits
- The Significance of Process Flow Diagrams
- A Brief Introduction to API RP 580
- API RP 580 Shortcomings
- A Glance at API RP 581
- The Risk Formula and Determining its Various Components
- Introducing an FRA Methodology for Process Piping and Pressure Vessels
DAY FOUR: RISK CODE DETERMINATION CASE STUDIES AND EXERCISES
- Risk Code Determination
- Inspection Interval Determination
- Piping Risk Determination Case Studies
- Pressure Vessels Risk Determination Case Studies
- Piping Risk Determination Exercises
- Pressure Vessels Risk Determination Exercises
DAY FIVE: PIPELINE FRA
- Relevant Pipeline Standards
- Pipeline Integrity Threat Categorisation
- Pipeline Segmentation Criteria
- Pipeline Inspection Intervals
- Pipeline Response Scheduling
Certificate Awarded
Upon successful completion of this training course, participants will be awarded a Certificate of Completion from XCalibre Training Centre, acknowledging their accomplishment. This certificate serves as a testament to their dedication to developing their skills and advancing their expertise in their respective fields.
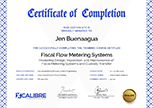