Date | Venue | Fee | |
---|---|---|---|
15 Sep - 19 Sep 2025 | Dubai – UAE | $ 4,950 | Register Now |
22 Jun - 26 Jun 2026 | Dubai – UAE | $ 5,950 | Register Now |
14 Sep - 18 Sep 2026 | Dubai – UAE | $ 5,950 | Register Now |
About the Course
In modern industrial maintenance management, the quest for efficiency and reliability is endless. Predictive maintenance, a maintenance management approach that aims to anticipate equipment failures before they occur, has emerged as a game-changer in the industry. At the heart of predictive maintenance lies' condition monitoring,' which offers a gateway to a new era of intelligent and data-driven maintenance practices. By continuously monitoring the health of machinery and systems, organisations can go beyond traditional reactive maintenance and embark on a path of predictability and optimisation.
Vibration analysis, thermography, oil analysis, ultrasound testing, and other cutting-edge techniques are at the forefront of this transformative journey, each contributing unique capabilities to the arsenal of predictive maintenance. These condition monitoring techniques provide real-time insights into the condition of equipment, enabling maintenance teams to detect early warning signs of faults and address them proactively, ultimately minimising downtime and maximising operational efficiency. Condition Monitoring allows maintenance or other actions to be scheduled to avoid failure consequences and limit consequential damages. It has a unique benefit in that conditions that shorten normal lifespan can be addressed before they develop into a major failure.
This 5-day dynamic Condition Monitoring Techniques training course is tailored for professionals seeking expertise in condition monitoring techniques to enhance equipment reliability and operational efficiency. Delegates will delve into a comprehensive exploration of various monitoring methodologies, instrumentation, and analysis tools. Through theoretical insights, hands-on exercises, and real-world applications, delegates will learn how to implement effective condition monitoring strategies in diverse industrial environments.
Core Objectives
Upon completing this training course, delegates will have a solid foundation in various condition monitoring techniques, enabling them to assess equipment health, detect potential issues, and implement proactive maintenance strategies. This knowledge will improve reliability, reduce downtime, and optimise maintenance costs in industrial settings.
The delegates will achieve the following objectives:
- Gain a comprehensive understanding of condition monitoring techniques and their role in asset management
- Acquire proficiency in utilising various condition monitoring technologies, including vibration analysis, thermography, and oil analysis
- Develop hands-on skills in effective data collection, interpretation, and utilisation for condition monitoring purposes
- Understand the fundamentals of lube oil analysis
- Learn the basics of various thermography analysis
- Demonstrate proficiency in signal analysis for condition monitoring
- Gain knowledge about measurement and characteristics of signals in condition monitoring
- Learn specific techniques for condition monitoring of pumps, compressors, engines, turbines, and motors
- Apply vibration-based fault detection and diagnostic techniques effectively
- Develop skills in advanced signal processing techniques and tools for condition monitoring
- Learn to detect, locate, and diagnose faults in rotating and reciprocating machinery using vibration analysis techniques (vibration, lube oil, thermography, and ultrasound)
Training Approach
The training course will blend theoretical sessions, practical hands-on exercises, case studies of real-world scenarios, and interactive discussions. Delegates will engage in practical exercises, simulating real-world scenarios to reinforce theoretical concepts. The approach aims to provide a holistic and immersive learning experience.
The Attendees
Likewise, it will be valuable to the professionals but not limited to the following:
- Maintenance Engineers
- Reliability Engineers
- Plant operators/Process engineers
- Condition Monitoring Technicians/Engineers
- Asset Managers
- Maintenance Supervisors
Daily Discussion
DAY ONE: INTRODUCTION TO CONDITION MONITORING
- Basic Principles
- Benefits
- Condition Monitoring Technologies
- Data Acquisition
- Vibration Sensors
- Data Collectors
- Sensor Mounting and Wiring
DAY TWO: VIBRATION ANALYSIS
- Time Waveform Analysis
- Frequency Analysis
- Spectral Analysis
- Enveloping
- Oil Analysis
- Sampling Techniques
- Testing Methods
- Interpretation Guidelines
DAY THREE: INFRARED THERMOGRAPHY AND ULTRASONIC TESTING
- Heat Transfer Basics
- Equipment and Measurement
- Applications
- Standards and Guidelines
- Principles
- Contact and Non-Contact Testing
- Interpretation Of Results
DAY FOUR: PERFORMANCE ANALYSIS, OIL ANALYSIS, AND WEAR DEBRIS MONITORING
- Importance of Lubricant Analysis
- Sampling Techniques and Oil Analysis Methods
- Wear Debris Analysis and Interpretation
- Oil Analysis for Predictive Maintenance
- Key Parameters Analysed and Interpretation of Results
- Viscosity – Measures the Oil's Thickness, Affecting Its Lubricating Ability
- Total Acid Number (TAN) and Total Base Number (TBN)
- Particle Count and Wear Metals
- Water Content
- Additive Concentrations
- Benefits of Oil Analysis
DAY FIVE: PERFORMANCE ANALYSIS
- Efficiency Testing
- Power Quality Assessments
- Process Parameter Monitoring
- Program Development
- Management Buy-in
- Goal and Budget Setting
- Creating Baselines
Certificate Awarded
Upon successful completion of this training course, participants will be awarded a Certificate of Completion from XCalibre Training Centre, acknowledging their accomplishment. This certificate serves as a testament to their dedication to developing their skills and advancing their expertise in their respective fields.
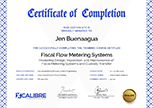