Date | Venue | Fee | |
---|---|---|---|
22 Sep - 26 Sep 2025 | London - UK | $ 5,950 | Register Now |
22 Dec - 26 Dec 2025 | Dubai – UAE | $ 4,950 | Register Now |
29 Jun - 03 Jul 2026 | Istanbul - Turkey | $ 5,950 | Register Now |
03 Aug - 07 Aug 2026 | Dubai – UAE | $ 5,950 | Register Now |
21 Sep - 25 Sep 2026 | London - UK | $ 5,950 | Register Now |
21 Dec - 25 Dec 2026 | Dubai – UAE | $ 5,950 | Register Now |
About the Course
How do you explain root cause analysis?
Failures of machines and equipment, both moving and static, have many causes. Some causes of failures appear to be immediate or, as seen by face value, but they may be superficial causes. The actual root causes may be hidden deep inside the components of machines and equipment in terms of material of construction, corrosion, stress processes, propagation of microstructure intergranular cracks, etc., or other associated aspects surrounding machines and equipment, in terms of operation, inspection, maintenance, methods, human-machine interface and the overall management around these amongst other factors.
Notwithstanding the causes of failure, incidents with Health, Safety, and Environment (HSE) outcomes from these machines and equipment failures while in service in the oil & gas industries are increasingly being seen globally. Such incidents result not only in severe human injuries but also fatalities resulting from major consequential incidents such as fire, explosion, toxic/lethal releases, etc. Depending upon the stakes and risks involved, the concerned industry must pay due attention to the root causes of such failures of the machines and equipment and do everything possible to prevent, minimise and contain these failures; else, quick escalation of incidents beyond the control of an organisation can wipe out the assets and end the business of a company.
This 5-day Root Cause Failure Analysis (RCFA) training course provides the organisation with a systematic methodology and actions to minimise or eliminate failures that ultimately harm people, damage equipment or property, cause loss of production, or have an adverse impact on the environment. By the end of the training program, delegates will be able to write an effective root cause failure analysis report.
Core Objectives
Delegates will possess the knowledge and practical skills to systematically investigate and identify root causes of failures. This training course will enable them to implement targeted solutions, enhance equipment reliability, and contribute proactively to prevent recurring issues in industrial operations.
The delegates will achieve the following objectives:
- Learn fundamental concepts around failures of machines and equipment, both moving and static
- Understand the relationship between failures of machines and equipment and the associated HSE incidents
- Comprehend failure mechanisms of various identified major machines and equipment
- Learn and use Root Cause Failure Analyses (RCA) to arrive at the root and generic causes of failures of machines and equipment
- Check the effectiveness of the implementation of CAPs and PAPs
- Understand and practice skills to draft and generate the RCFA Report
- Comprehend the importance of RCFA Close-out
- Cascade lessons learned from the failure Incident and the RCFA Report
- Address the various Insurance, Legal, and Statutory Implications accurately
Training Approach
The training course will adopt a hands-on and interactive approach, combining theoretical sessions, case studies, group discussions, and practical exercises. Real-world scenarios and case studies will simulate the RCFA process, ensuring a realistic and immersive learning experience.
The Attendees
This training course is essential for anyone challenged to manage data quality, business processes, or people and organisations. Understanding why is the key to knowing what to do—the core of sound decision-making. But cause-and-effect relationships are elusive. Real causes are often difficult to find, so we settle for easy answers. This leads to fixing symptoms rather than solving problems and to little or no gain where opportunity is abundant.
Likewise, it will be valuable to the professionals but not limited to the following:
- Inspector, Maintenance, and HSE Professionals at All Levels
- Middle and Senior Management
- All line functions at All Levels
- Senior Managers and Managers in Operation, Maintenance, Inspection, Engineering, Other Line Disciplines
- Non-line functions such as office managers and finance professionals dealing with insurance and statutory compliances
Daily Discussion
DAY ONE: FUNDAMENTAL CONCEPTS AND SOME FAILURE ANALYSIS TOOLS
- Reliability Engineering and Predictive Maintenance
- Failure Mode Effects Analysis
- Fault-Tree Analysis
- Cause-and-Effect Analysis
- The Fishbone Graph
- Sequence-of-events Diagram
- Bow-Tie Method
- Introduction to Root Cause Failure Analysis
- Purpose of RCFA
- Effective Use of RCFA
- Personnel Requirement
- Conditions for Using the Method
DAY TWO: ROOT CAUSE FAILURE ANALYSIS METHODOLOGY
- Reporting a Failure Incident or Problem
- Symptoms and Boundaries/Conditions
- Perceived Causes of Problem
- Event-Reporting Format
- Failure Incident Classification
- Typical Failure Incident-Reporting Form
- Equipment Damage or Failure
- Operating Performance
- Economic Performance
- Safety
- Regulatory Compliance
- Data Gathering: Interviews, Questions to Ask
- Collecting Physical Evidence
- Analyse Sequence of Events
- Design Review: Minimum Design Data
- Objectives of the Design Review
- Application and Maintenance Review: Installation, Operating Envelope, SOPs
- Maintenance History and the Associated Procedures and Practices
- Observations & Measurements: Vibration Analysis, Process Parameters, Visual Inspection, Measurement Devices, Failed Machine Components, Wear Particles
DAY THREE: DETERMINING THE FAILURE ROOT CAUSES
- Misapplication
- Poor Design Practices
- Aging: Depreciation, Remainder Life, Replacement Planning not Predictive
- Procurement Practices: Inadequate Specifications, Substitutions, Low Bid vs Lifecycle Cost, Vendor Evaluations
- Poor Operating, Inspection & Maintenance Practices and Procedures
- Poor Training
- Inadequate Supervision
- Ineffective Communication
- Faulty Human Engineering
- Work Environment: Physical and Psychological
- Management Systems
- Substandard Qualify Control
DAY FOUR: REPORT AND RECOMMENDATIONS
- Failure Incident Summary
- Initial Plant Condition
- Initiating Event
- Failure Incident Description
- Immediate Corrective Actions
- Causes and Long-Term Corrective Actions
- Internal and External Reports Filed
- References and Attachments
- Failure Investigator or Investigating Team Description
- Review and Approval Team Description
- Distribution List
- Verification of Implementation of Corrective Action and Its Effectiveness
DAY FIVE: DESIGN EVALUATION ASPECTS AND LIVE FAILURE INCIDENTS
- Preventive Troubleshooting for any Machine & Equipment to Avoid Failures
- Developing an Effective Root Cause Analysis Plan: Steps and Considerations
- Building and Managing Cross-Functional Root Cause Analysis Teams
- Strategies for Conducting thorough Root Cause Analysis Investigations
- Best Practices for Facilitating Root Cause Analysis Meetings and Workshops
- Implementing Solutions and Preventive Measures to Address Root Causes
- Monitoring and Evaluating the Effectiveness of Implemented Solutions from Real-world Case Studies
- Driving Continuous Improvement
Certificate Awarded
Upon successful completion of this training course, participants will be awarded a Certificate of Completion from XCalibre Training Centre, acknowledging their accomplishment. This certificate serves as a testament to their dedication to developing their skills and advancing their expertise in their respective fields.
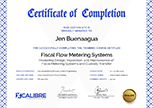