Date | Venue | Fee | |
---|---|---|---|
29 Sep - 03 Oct 2025 | London - UK | $ 5,950 | Register Now |
17 Nov - 21 Nov 2025 | Dubai – UAE | $ 4,950 | Register Now |
15 Dec - 19 Dec 2025 | Kuala Lumpur - Malaysia | $ 5,950 | Register Now |
02 Feb - 06 Feb 2026 | Dubai – UAE | $ 5,950 | Register Now |
06 Apr - 10 Apr 2026 | London - UK | $ 5,950 | Register Now |
04 May - 08 May 2026 | Dubai – UAE | $ 5,950 | Register Now |
06 Jul - 10 Jul 2026 | London - UK | $ 5,950 | Register Now |
28 Sep - 02 Oct 2026 | London - UK | $ 5,950 | Register Now |
16 Nov - 20 Nov 2026 | Dubai – UAE | $ 5,950 | Register Now |
14 Dec - 18 Dec 2026 | Kuala Lumpur - Malaysia | $ 5,950 | Register Now |
About the Course
API RP 982, "Management of Hazards Associated with Location of Process Plant Portable Buildings," is a comprehensive guideline developed by the American Petroleum Institute (API) to address the safe placement and management of portable buildings within process plant facilities. This 5-day API 982 - Refractory Inspector training course provides essential guidance on identifying and mitigating hazards associated with the location of these buildings, ensuring the safety of personnel and operations in industrial settings. It begins with an in-depth exploration of the scope and purpose of API RP 982, emphasizing its applicability to various types of process plants, including refineries, chemical plants, and petrochemical facilities. Delegates gain insights into the regulatory framework and industry standards that govern the placement of portable buildings, enhancing their understanding of compliance requirements and best practices.
This training program will cover hazard identification methodologies specific to portable buildings, risk assessment techniques for evaluating potential hazards, and strategies for implementing effective hazard control measures. Delegates learn to assess environmental factors, such as proximity to process equipment, potential for exposure to hazardous substances, and impact on emergency response procedures. It explores practical case studies and real-world examples that illustrate the application of API RP 982 principles in different industrial scenarios. Through interactive sessions and workshops, delegates engage in hands-on exercises to apply hazard management strategies, conduct site assessments, and develop mitigation plans tailored to specific operational contexts.
Delegates will possess a comprehensive understanding of API RP 982, enabling them to contribute effectively to designing and managing portable buildings within process plant environments safely. This knowledge equips them to enhance safety protocols, mitigate risks associated with building placement, and ensure compliance with industry standards, ultimately fostering a safer working environment for all personnel involved in industrial operations.
Core Objectives
The delegates will achieve the following objectives:
- Understand what refractories are and why they are important
- Comprehend which damage mechanisms are possible and how to recognise them
- Master the inspection options and when to apply them
- Understand specific issues for different industrial application cases
- Analyse and interpret inspection results, both offline and online
Training Approach
This training course integrates theoretical knowledge with practical application to ensure a thorough grasp of API RP 982 and refractories. Whether conducted in a classroom or virtually, it emphasize interactive learning through case studies and real-world examples. Delegates actively engage in hands-on workshops applying API guidelines to simulated industrial scenarios, reinforcing their understanding through practical exercises.
It provides deep insights and facilitates discussions on complex subjects, fostering collaborative learning environments. It prioritizes developing problem-solving and critical thinking skills and equips delegates to address real-world refractory management and damage assessment challenges. This approach ensures that each delegate gains practical skills for enhancing safety and operational efficiency in industrial settings.
The Attendees
This training course comprises a diverse group of professionals crucial to ensuring the integrity and efficiency of refractory systems in industries such as oil & gas, petrochemicals, and power generation. They range from inspectors and engineers to managers and consultants, all dedicated to maintaining high standards of safety, performance, and compliance in refractory operations.
Likewise, it will be valuable to the professionals but not limited to the following:
- Refractory Inspectors and Engineers
- Quality Control Personnel
- Maintenance Engineers
- Plant Managers
- Project Engineers
- Safety Officers
- Pressure Equipment Inspectors
- Asset Integrity Managers
- QA/QC Inspectors
- Professionals working in Refractory Production and Application
Daily Discussion
DAY ONE: REFRACTORIES INTRODUCTION
- Use of Refractories in Different Environments
- Function of Refractories
- Thermal Protection
- Energy Retention
- Abrasive and Aggressive Environment Protection
- Classification of Refractories
- Grouping of Types of Equipment Using Refractory
- Refractory Design Specifications
- Refractory Materials Specifications
- Key Material Properties and Their Significance
- Refractory Installation and Inspection
- Related Standards and Data
DAY TWO: API RP 982 INTRODUCTION
- API RP 982 Overview
- Scope and Definitions
- Responsibilities and Safety Requirements
- Inspection and Assessment of Refractory Linings
- Initial Inspections
- Inspection Methods
- Visual, Hammer Test
- Mechanical Tests
- Thermography/Infrared
- Partial Tear Out
- Remote Visual (Limitations)
- Thickness Verification
- Radiography
- Remaining Life Calculation (Erosion Loss)
- Exploratory Removal, Sampling, and Testing
- Refractory Lining Defects and Degradation Mechanisms
- Refractory Lining Degradation Example Images
- Case Study: Identifying Damage Mechanisms, Interpreting Inspection Results
DAY THREE: API RP 982, API 560 REQUIRED KNOWLEDGE
- Damage Mechanisms of Castable Refractory: Cracking, Spalling, Laminations, Erosion, Corrosion/Chemical Attack, Coke Induced Failure Mechanisms, Overheating, Gas Bypassing/Flow Behind Refractory
- Degradation in Brick Refractory: Creep, Structural Movement, Coke Impregnation, Overheating
- Degradation in Anchor Systems: Anchor Failure, Fatigue, High-Temperature Corrosion, Mechanical Failure, Weld Attachment Failure
- Failure Modes of Fiber, Multi-layer Refractory Systems, and Special Components such as Ferrules and Tiles
- Marking System for Inspection, Overview, and Documenting
- Critical Activities During Refractory Installation
- Documentation of Refractory Installation
- Quality Control for Installation and Different Types of Refractories
- Refractory Lining Degradation Mechanism Matrix
- API Certification for Refractory Inspection Personnel
- API STD 560 Requirements: Chapter 11 - Refractory Linings, Firebrick Layer Lining, Gravity Wall Construction, AES/RCF Fiber Construction, Castable Layer Design, Anchors and Anchor Hardware Components
- API STD 560 Requirements: Refractory QA/QC, Examination, Testing, corresponding annexes
- Case Study: Identification of Damage, Remaining Life Calculation
DAY FOUR: BODY OF KNOWLEDGE ADDITIONAL DOCUMENTS AND USE OF REFRACTORIES IN REFINING ENVIRONMENT
- API Publication 935: Thermal Conductivity Measurement Study of Refractory Castables
- API Technical Report 977: ASTM C704 Test Variability Reduced to Allow Further Optimisation of Erosion-resistant Refractories for Critical Oil Refining Applications
- API Technical Report 978: Monolithic Refractories: Manufacture, Properties, and Selection
- API Technical Report 979: Applications of Refractory Lining Materials
- API Technical Report 980: Monolithic Refractories: Installation and Dryout
- API Technical Report 981: Thermal Expansion Under Load and Creep of Refractories, Evaluation and Comparison of Testing Methods
- Use of Refractories in Refining Environment: Furnaces, Boilers, Chimneys, Reactors, Regenerators, FCC Plants, Internal Reactors, Gas Strippers, Transfer Lines, Slide Valves, Heaters, Gasifiers, Sulfur Furnaces, Other Uses
- Case Study: Assessment of Damage for FCC Reactor Case
DAY FIVE: REFRACTORIES IN OTHER INDUSTRIES, TESTING
- Use of Refractories in the Conventional Power Industry
- Use of Refractories in Chemical Industries
- Use of Refractories in Steel-making Processes
- Use of Refractories in the Cement Industry
- Use of Refractories in Other Industries: Carbon Black Production
- Examination Questions Overview
- Mock Examination
Certificate Awarded
Upon successful completion of this training course, participants will be awarded a Certificate of Completion from XCalibre Training Centre, acknowledging their accomplishment. This certificate serves as a testament to their dedication to developing their skills and advancing their expertise in their respective fields.
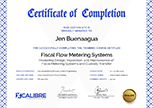