Date | Venue | Fee | |
---|---|---|---|
09 Feb - 13 Feb 2026 | Dubai – UAE | $ 5,950 | Register Now |
04 May - 08 May 2026 | Dubai – UAE | $ 5,950 | Register Now |
06 Jul - 10 Jul 2026 | London - UK | $ 5,950 | Register Now |
About the Course
A comprehensive understanding of Fitness-for-Service (FFS) concepts and technologies focusing on the application of API 579-1/ASME FFS-1 published jointly by the American Petroleum Institute (API) and the American Society for Mechanical Engineers (ASME), this standard addresses a broad spectrum of flaw types and damage mechanisms. The primary objective of API 579-1/ASME FFS-1 is to establish criteria that ensure safe and reliable operation of equipment, aligning with foundational design codes such as ASME Boiler and Pressure Vessel Code (BPVC), ASME Piping codes, and API design and inspection codes.
The 5-day API 579-1/ASME FFS-1 Fitness-For-Service Evaluation training course is a structured approach to flaw evaluation, acceptance criteria, and calculation of remaining life. It delineates three levels of evaluation. Level 1 involves procedures for evaluating flaws detailed in Parts 3 through 14, illustrated through practical examples. Level 2 procedures are discussed, accompanied by worked examples, while an introduction to Level 3 analysis methods and acceptance criteria is provided. It also covers stress categories and failure modes associated with each, elucidating their implications.
Moreover, fundamental aspects of pressure vessel, piping, and storage tank design are addressed, including relevant code-design formulas for determining required thickness, which is demonstrated through example problems. Throughout, emphasis is placed on ensuring that all FFS assessments comply with applicable codes and regulatory requirements while upholding basic engineering principles and understanding the intended scope of reference publications. This approach guarantees that equipment remains operationally sound and meets stringent safety standards in industrial applications.
Core Objectives
The delegates will achieve the following objectives:
- Utilise API 579-1/ASME FFS-1 guidelines to assess various flaw types and damage mechanisms in equipment
- Perform Level 1 flaw evaluations using prescribed acceptance criteria and calculation methods
- Execute Level 2 flaw assessments through practical worked examples and case studies
- Describe the fundamental stress categories and failure modes affecting equipment integrity
- Analyse and interpret Level 3 FFS analysis methods and their implications for equipment reliability
Training Approach
This training course employs a blended approach, combining interactive sessions with practical case studies and real-life examples. Delegates will explore API 579-1/ASME FFS-1 standards through instructor-led discussions and demonstrations. Real-life case studies illustrate application scenarios, enhancing understanding of flaw evaluation and remaining life calculations. It emphasizes hands-on learning with practical exercises that simulate Level 1 and Level 2 evaluations, ensuring delegates grasp and apply theoretical concepts effectively. This methodological approach integrates research-backed principles with industry best practices, fostering a deep comprehension of Fitness-for-Service methodologies essential for safe and efficient equipment operation in the refining, petrochemical, and petroleum industries.
The Attendees
This training course is designed for professionals seeking to enhance their expertise in Fitness-for-Service assessments and ensure the safe and efficient operation of industrial equipment.
Likewise, it will be valuable to the professionals but not limited to the following:
- Engineers (Mechanical, Process)
- Inspection and Maintenance Engineers
- Asset Integrity Managers
- Process Safety Engineers
- Mechanical equipment designers
- Safety Engineers
Daily Discussion
DAY ONE: INTRODUCTION TO FITNESS-FOR-SERVICE ENGINEERING ASSESSMENT PROCEDURES
- Introduction to Construction Codes and Fitness-For-Service Scope
- Organisation, Responsibilities, and Qualifications
- Fitness-for-Service Engineering Assessment Procedures
- Applicability and Limitations of FFS Assessment Procedures
- Introduction to Level 1, 2, and 3 Assessments
- Acceptance Criteria and Documentation
- Remaining Life Assessment and Guidance
- Basic Calculation Formulas and Data
- Thickness, MAWP, and Stress Equations for FFS Assessment
- Stress Analysis Overview
- Material Properties for Stress Analysis
- Workshop: Stress and Thickness Calculations for Various Geometries
DAY TWO: FFS ASSESSMENT OF BRITTLE FRACTURE AND GENERAL METAL LOSS
- Evaluation and Resistance to Brittle Fracture
- Supplemental Assessment to FFS Procedures
- Critical Exposure Temperature (CET) and Minimum Allowable Temperature (MAT)
- Level 1, 2, and 3 Assessments for Different Systems
- Assessment of General Metal Loss and Thickness Averaging
- Data Requirements and Assessment Techniques
- Remaining Life Assessment and In-Service Monitoring
- Workshop: Pressure Vessel and Piping Examples
DAY THREE: FFS ASSESSMENT OF LOCAL METAL LOSS, PITTING, AND BLISTERING
- Assessment Procedures for Local Metal Loss
- Calculation of MAWPr and MFHr
- Assessment of Pitting Corrosion and Blister Arrays
- Level 1, 2, and 3 Assessment Techniques
- Remaining Life Assessment Approaches
- Workshop: Pressure Vessel, Atmospheric Tank, Elbow Examples
- Assessment of Hydrogen Blisters and Damage
DAY FOUR: ASSESSMENT OF CRACK-LIKE FLAWS
- Assessment Procedures for Crack-Like Flaws
- Data Requirements and Assessment Techniques
- Residual Stresses and Crack Opening Areas
- Material Properties and Stress Analysis
- Subcritical Crack Growth and Leak-Before-Break Analysis
- Workshop: Pressure Vessel and Piping Examples
- Assessment of Laminations, Weld Misalignment, and Shell Distortions
- Assessment of Dents, Gouges, and Dent-Gouge Combinations
DAY FIVE: FATIGUE DAMAGE AND CREEP: FIRE DAMAGE ASSESSMENT
- Assessment Procedures for Fatigue Damage
- Calculation of MAWP and Coincident Temperature
- Remediation and In-Service Monitoring for Fatigue
- Assessment of Components in the Creep Range
- Microstructural Approaches and Life Assessment
- Workshop: Simple Assessment Examples
- Assessment of Fire Damage and Process Upsets
- Remediation Techniques and Documentation Requirements
Certificate Awarded
Upon successful completion of this training course, participants will be awarded a Certificate of Completion from XCalibre Training Centre, acknowledging their accomplishment. This certificate serves as a testament to their dedication to developing their skills and advancing their expertise in their respective fields.
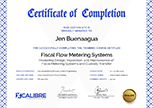